INTRODUCTION
Ubisense have been providing location solutions to many customers over the last 17 years. These solutions have been delivered with a mixture of hardware and software.
The hardware – Dimension4™ – is Ultra Wide Band (UWB) and is the most accurate industrialised real time location solution (RTLS) available. Ubisense are now supporting many hundreds of thousands of tags and sensors deployed across many markets.
The software – SmartSpace® – takes the data from any location solution, whether UWB, RFID, bluetooth, barcode, or derived location and places the tracked asset into an accurate 3D model of the customer’s facility. SmartSpace then enables location or business rules to be applied to the asset to help control its process or related processes across the business. The software is also generally integrated to existing customer business systems ensuring that the visualisation of the assets in the model are fully meaningful.
SmartSpace enables customers to view their business and operational processes real time with built in controls to ensure best practice processes are adhered. As a result, Ubisense customers have been able to improve their processes and have become much more efficient and productive. Ubisense are now working within the Aircraft Maintenance environment and helping customers in this sector to achieve the same.
The use cases I will describe in this series are based on real scenarios in the Airframe Heavy Maintenance industry and I am sure that most of you who are working in this sector will relate to each described scenario. Benefits that have been achieved are significant and customers continue to improve their efficiency and related productivity.
SMARTSPACE USE CASE – WORK ORDER MANAGEMENT
Current situation
When a 3rd party MRO company wins a contract to complete heavy maintenance on an aircraft, the process to create the work pack starts some months prior to the aircraft arriving at the MRO hangar. The tasks to be completed are agreed along with the contract terms. This work can contain hundreds of tasks that need to be meticulously planned. This is generally completed by a planning department with personnel who understand the process and the aircraft to be worked on.
Normally, MRO companies will use specialised software to build and execute the plan. Some examples of this specialised software are AMOS, TRAX, Mxi, Rusada, Ramco etc. A final draft plan is completed prior to the aircraft arriving at the facility and initial meetings are held between the planning department and the execution team to ensure the planned check is workable.
Once agreed, operations take over the management of the work order. If the business operates using paper cards, they print the cards out and order them generally in a rack as shown in the image.

Areas that can be improved
Many MRO companies have introduced manual systems or processes to manage the complexities and interactions between the tasks, technicians, tooling and material. This generally involves daily or shift review meetings, detail project plans and other adhoc activities.
The review meetings become a crucial way for management to stay on top of each work order to ensure minimal slippage. This is mainly due to the unforeseen issues that can arise within each work order. I have been involved in meetings that involved between 5 and 10 people each time and the meeting time-span ranges between 15 min to more than an hour. Examples of these unforeseen issues include:
- unexpected non-routine issues discovered during early inspections e.g. corrosion
- material shortages
- skill shortages
If the work order had no unforeseen issues then the review meetings would not be unnecessary. Unfortunately, most work orders have these types of issues.
Most companies will create a project plan either as an embedded plan in the MRO software or as a separate plan in the project planning software. At one company I worked with, each check was managed by 2 project managers to ensure the overall work order was completed to plan. Every time there was a change to the plan, a new plan was redrafted for the supervisors and technicians to follow.
The whole overview and management process is very labour intensive but necessary because most companies do not have the visibility of what is actually happening in the work order.
How the issues were addressed by Ubisense
Ubisense has addressed these complex and valuable work orders (these can be more than £250k per work order) by focusing on the underlying business processes.
The first issue addressed was the lack of visibility of the progress to management and others, and issues being discovered during the work order.
The second issue was the impact that the unforeseen issues would have on the overall work order – i.e. will the work order still be able to be completed in the same timescale.
The third issue was the lack of a common communication system where any issues raised were clearly identified, described, actioned, where responsibility for the action was clearly identified, and where a resolution to the issue was also clearly articulated and added to the communication system.
Once each of these issues were addressed there was no further need to have the regular review meeting. The issues were addressed in real time with full visibility to all who needed to see the impact and/or the resolution.
SmartSpace enabling benefits
SmartSpace is a location based solution and as such each entity in the solution requires an x, y, z location. The first phase of any SmartSpace solution is the development of an accurate 3D model of the customer’s hangar. In the model, we develop rules that define what the assets we place in the model can or cannot do. SmartSpace also integrates with the customers existing solutions including MRO, ERP, HR etc. and uses the existing data through integration to help manage the work orders effectively.
In this particular use case, we have a model of a hangar and a model of the aircraft to be placed in the hanger to which the work order applies.
Each task that has been planned for this particular work order could be visualised in the Planning Office of the model while it is being developed since that is where the x, y, z coordinates of the tasks will be. Once the work order is released, the tasks move to the supervisor’s office and either immediately or when the supervisor displays them on his board will be visualised on the electronic task board. This can be seen by anyone with access to the SmartSpace solution.
As the supervisor issues the tasks or the technicians select them, the tasks move to the relevant zone on the aircraft or to a general area defined by the customer. Every task has a working location that is related to the aircraft or hangar. Since we know the aircraft’s location in the hangar, we can now display on the hangar model where these tasks are and who is working on them. This then lets management or anyone with the right level of access to SmartSpace have a bird’s eye view of the check as it is being completed.

Through the SmartSpace business rules the activities can be colour coded to highlight any non-routines and also whether they were expected non-routines or unexpected non-routines. This provides the real time view and status of each work order as it is being completed.
The second issue that was addressed was to provide management and users visibility of the impact to the work order that unforeseen issues may have on the execution plan. Using the business rules within SmartSpace, and through these rules enabling customers to connect tasks with related tasks, ensures any impact affecting one part of a series of linked tasks will affect all linked tasks. This then continually reviews and re-plans the work order real time taking into account any unforeseen issues that have been discovered. In addition to the continual re-planning, an on time metric is included in the dash board to provide management with the Turn-Around-Time (TAT) metric and on-time performance. Therefore, management can now see real time what is happening during the work order and what impact any unforeseen issues may have on the overall work order.
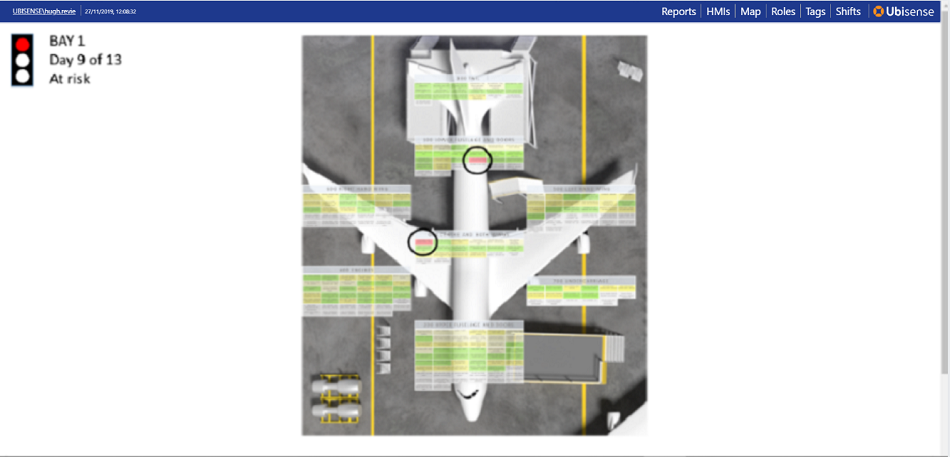
Finally, the third issue is addressed again using the business rules that define who should be responsible for actioning any unforeseen issues. The moment an unforeseen issue is discovered, the business rules kick in with a message to the responsible person. Metrics are in place within SmartSpace to provide an escalation in the event that the responsible person does not action within the specified time scale set up by the customer, and ensure appropriate timely action is recorded and visible to all who need to see it. This provides an auditable and traceable record of the process not only of finding the unforeseen issue but also the actioned record. This information would generally be transferred to the MRO solution as a permanent record.
SmartSpace therefore enables all those involved in the management process to see at every stage of a work order how it is performing and whether it will be completed on time.

Do you want to learn more on How to Improve Business Efficiency in an Aerospace MRO Environment? Watch Dr Hugh Revie’s On-Demand Webinar on the same topic: WATCH NOW

Written by Dr Hugh Revie, Sales Director Aerospace EMEA at Ubisense
Hugh is one of the world’s leading experts in the Aerospace industry. Hugh has now been working in Aerospace for more than 30 years and, prior to joining Ubisense, started his career in aviation after graduating with a doctorate in Engineering and, initially working for British Aerospace. Around 18 years ago, he created his own company, CoreData Limited, focused on helping airlines, MROs, OEMS and aircraft supply chain companies with solutions that could drive value from the large amounts of data they were accumulating. He finally sold the company to Rolls Royce. Since then he has been working with customers to improve efficiencies by using their own data and continues to do this with Ubisense.